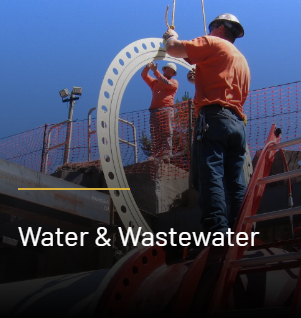
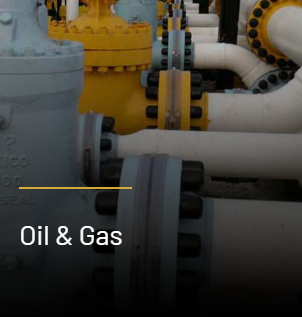
Process Improvement Need Creates ERP System Improvements and Sizable Cost Savings
Company Profile
Advance Products & Systems, LLC, (APS) founded in 1978, is a leading manufacturer and distributor of corrosion prevention and protection products in the water & wastewater, oil & gas, industrial & mechanical, and chemical pipeline industries. APS products are manufactured for these industries to prevent and protect against unwanted corrosion. APS also offers quality safety products manufactured to meet customers’ needs to protect personnel, equipment, and the environment.
APS has experienced steady growth over the years and presently has 65,000 square feet of manufacturing space, and currently employs over 130 full-time employees. A complete inside sales staff and office support system are here to satisfy representatives and distributors in the United States, Canada, Mexico, South America, Europe, Middle East, Southeast Asia and several other regions. The corporation’s end users include municipalities, public utilities, oil and gas companies, and other industrial and commercial firms.
Situation
Advance Products & Systems was familiar with the Manufacturing Extension Partnership after having utilized our services for many needs to include an Energy Assessment, COVID-19 Assessment, Sales Training and more. Advance Products & Systems reached out to the team at LCTCS MEP of LA for Process Improvement needs and ultimately signed up for 5S Training. During this initial meeting, APS also took the Supply Chain Assessment and the concerns noted for the company were limited suppliers for particular products/materials, long lead times, and some products only being available to them overseas.
Solution
As a result of the recent projects, Advance Products & Systems management requested two follow-up executive coaching sessions to address the company’s challenges with their current ERP system. Following two executive coaching meetings with APS management and VersoriumIQ, resources were located to assist APS with coaching/training to better utilize their current ERP system resulting in cost avoidance of several hundred thousand dollars.
“We are continuing to explore further opportunities for advancements by way of automation and through the vast network of LCTCS MEP of LA. Their broad reach across the nation is proving to be very beneficial!”
—Kidd Culotta, Manager
Results
The executive coaching meetings ultimately led APS to save several hundred thousand dollars by helping them to navigate through their frustrations with their ERP software. Without this help, APS would possibly incurred the costs of several hundred thousand dollars unnecessarily. This discovery has also led to 5S Training and Lean Kaizen Implementation for the company as well as Lean Manufacturing Training to continue to improve their growing business. As a result of the Supply Chain Assessment, additional challenges were identified that impacted the company’s supply chain and logistics. This led to a conversation with LCTCS MEP of LA’s third-party provider supply chain experts to resolve issues with their ERP system. The 3PP provided additional industry users with the same software which were able to provide solutions to improve APS’s ERP efficiency. This solution also led to APS choosing to keep their current ERP system and ultimately led them to realize a cost avoidance of several hundred thousand dollars not having to invest in a new ERP system or train employees on another software platform.
IT Systems/Software Investment
Jobs Created/Retained
Plant/Equipment Investment
Workforce Investment